The ubiquity of PCBs in our daily lives continues to expand, and this growth is largely driven by consumer demand for smarter products that can monitor or control more common activities in which we engage, as well as industry demand . For example, in aerospace, medical devices, automotive, and commercial electronics, industry needs include enhanced functionality and capabilities. These needs have been met through the utilization and development of new materials, new components, and manufacturing techniques, and PCB manufacturing processes and equipment must continue to evolve.

HDI
High Density Interconnect (HDI) was developed to meet the demand for ever smaller and more powerful products, especially when it comes to routing. This feature reduces the number of layers in the PCB stackup and facilitates high-speed signal transmission. High-density interconnect manufacturing faces the challenge of making traces so that more traces can be routed in a smaller area, which introduces issues such as noise and interference. The expansion of this concept, interconnect per layer and interconnect at any layer should also continue to grow in the coming years.
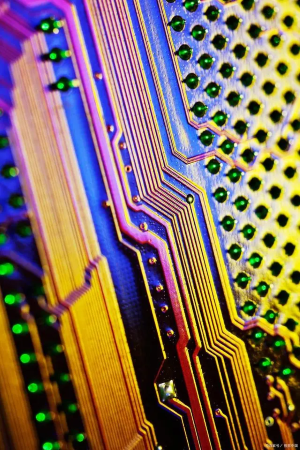
High power boards (48V and higher)
There is a big push for higher power PCBs. This includes boards with up to 48V power supplies. These voltage levels are in response to the increase in solar energy, with solar panels typically operating at 24V or 48V, and electric vehicles (EVs) which can run as high as hundreds of volts. These high-power boards require PCBs to accommodate larger components such as battery packs while being able to handle interference issues efficiently.
internet of things
The Internet of Things (IoT) is a multilayer design strategy that requires fast communication (often wireless) between layers and elements. This is the key technology behind smart homes and offices, as well as remote monitoring. A major manufacturing challenge for IoT PCBs is meeting the various standards and regulations governing their development.
Flexible PCB
Flex and Rigid – Flex PCBs are rapidly gaining market share in PCB development. In fact, it is predicted that by the mid-2020s, one-third of all manufactured PCBs will be flexible. The advantages of flexible boards include higher performance, smaller size, higher reliability and more material choices. However, before choosing a material, one should understand the key properties that affect flex manufacturing.

off-the-shelf commercial components
Another popular trend is to use off-the-shelf commercial components or COTS components, the use of COTS components brings some standardization and reliability issues. Components used in space manufacturing have traditionally been heavily scrutinized, and commercialization of the industry could lead to less regulation of components.
Parts Supply Chain Control
The increased use of electronics has also fueled the need for improved security, with a major focus on eliminating counterfeit components from the supply chain, which is especially important for critical system manufacturing. The ability to address this problem is continually being improved with advanced technologies, including virtual reality (VR) and augmented reality (AR) simulations during PCB assembly.