Catalog
Introduction
Understanding Flex PCBs
Design Considerations for Advanced Flex Circuits
Manufacturing Processes and Techniques
Applications of Advanced Flex Circuits
Future Trends and Innovations
Conclusion
Introduction to Advanced Flex PCBs
The world of electronics has continually evolved, leading to the development of flexible printed circuit boards (Flex PCBs), a cornerstone in modern electronic design. These advanced circuits have revolutionized the way we approach electronic hardware design, offering unprecedented flexibility and reliability.
Flex PCBs have become integral in various applications, from simple PCB board projects to complex microcontroller PCB designs. Their ability to conform to different shapes and sizes while maintaining functionality makes them a preferred choice for many best PCB manufacturers, including those specializing in PCBA manufacture and turnkey PCB assembly.
Understanding Flex PCBs
Flex PCBs are known for their adaptability, made possible by flexible, high-quality materials like polyimide. These materials allow the PCBs to bend and flex during use, a significant advantage over traditional rigid PCBs. This flexibility opens up new avenues in electronic design, particularly in applications where space is at a premium.
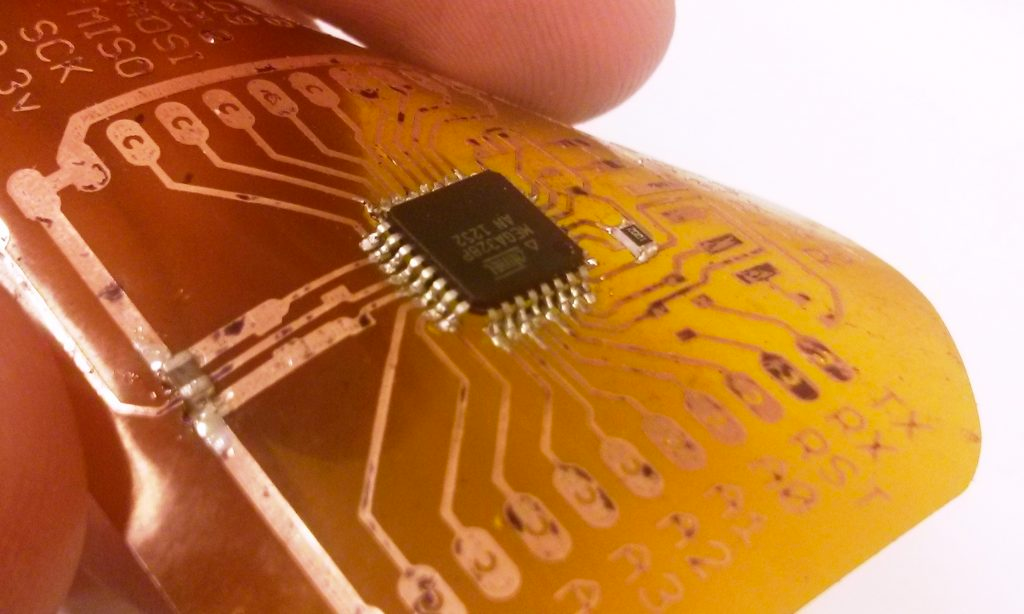
Flex PCB manufacturer often highlights the durability and space-saving features of these boards, making them ideal for a wide range of applications, including wearable technology and compact electronic devices. The best PCB manufacturers in China are known for their expertise in crafting these advanced flex circuits, combining quality with cost-effectiveness.
Design Considerations for Advanced Flex Circuits
When designing advanced flex circuits, it’s crucial to consider various factors that affect performance and reliability. This includes understanding the mechanical stresses that flex PCBs will undergo and choosing appropriate materials and trace layouts. PCB design services often involve sophisticated software tools to simulate and optimize these designs.
The challenges in designing these PCBs are numerous, but the rewards are significant. By utilizing PCB layout services, designers can create more efficient and compact designs, paving the way for innovations in electronics, such as sophisticated IoT devices and advanced medical equipment.
Manufacturing Processes and Techniques
The manufacturing process of flex PCBs involves several advanced techniques, like laser drilling and the creation of microvias, to meet the demands of complex electronic designs. The best PCB manufacturers have honed these processes to produce high-quality boards that meet stringent standards.
Quality control is paramount in the production of flex PCBs. Printed circuit board assembly facilities conduct thorough testing to ensure that each board functions correctly under various conditions. This meticulous approach is what sets apart top-tier PCB assemblers and manufacturers.
Applications of Advanced Flex Circuits
Flex PCBs, with their unique blend of flexibility, durability, and lightweight design, have opened up a world of possibilities in various industries. Let’s explore some of the most impactful applications of these advanced circuits.
Medical Devices
In the medical sector, the application of Flex PCBs has been a game-changer. Their small footprint and flexibility are crucial in devices like hearing aids, pacemakers, and advanced diagnostic equipment. Flex circuits can conform to the ergonomic shapes required by wearable medical devices, making them more comfortable for patients. This adaptability is not only beneficial for patient comfort but also enhances the performance of the devices, allowing for more accurate readings and monitoring.
Moreover, in the realm of medical implants, Flex PCBs are invaluable. Their ability to withstand the harsh conditions of the human body, coupled with their biocompatibility, makes them ideal for long-term implantable medical devices. These applications demonstrate the unique capabilities of Flex PCBs in sensitive and critical applications, where reliability and precision are paramount.
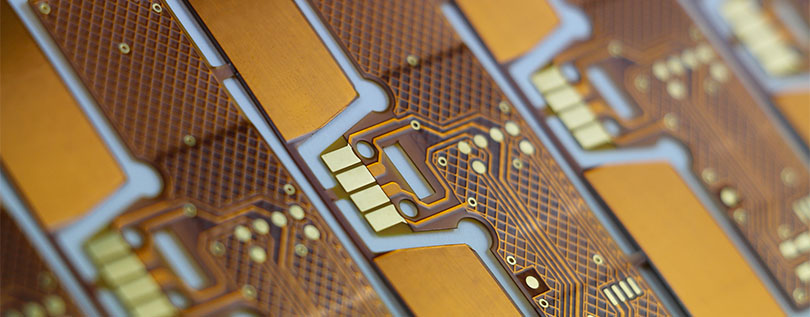
Aerospace and Defense
In aerospace and defense, the robustness and reliability of Flex PCBs are put to the test. These industries demand components that can endure extreme conditions, such as high vibration, significant temperature variations, and limited space. Flex PCBs are used in everything from satellites to fighter jets, where their lightweight nature contributes to overall efficiency and performance. In satellites, for instance, Flex PCBs are essential for creating compact, complex wiring that can withstand the rigors of space travel.
Flex circuits also play a pivotal role in modern defense systems. They are used in advanced communication devices, control systems, and even in wearable technology for soldiers, providing them with lightweight and durable electronics that enhance their capabilities on the field.
Consumer Electronics
The consumer electronics industry perhaps best demonstrates the versatility of Flex PCBs. From smartphones and tablets to wearable tech like smartwatches and fitness trackers, Flex PCBs have enabled the miniaturization of devices without compromising performance. Their ability to bend and fold has been crucial in developing foldable or curved screen devices, pushing the boundaries of what’s possible in consumer technology.
Furthermore, Flex PCBs are integral in developing compact, high-performance cameras, portable gaming devices, and even in advanced audio equipment. Their reliability and adaptability make them perfect for these applications, where user experience and device longevity are key considerations.
Automotive Industry
In the automotive sector, Flex PCBs are revolutionizing the way vehicles are designed and function. With the shift towards electric and autonomous vehicles, the demand for reliable and compact electronic components has surged. Flex PCBs are used in a range of applications, from control systems and LED lighting to sensors and displays. They are particularly valuable in creating more efficient and compact wiring layouts, reducing overall vehicle weight, and improving fuel efficiency.
Advanced driver-assistance systems (ADAS) heavily rely on Flex PCBs for their sensor and camera systems. These circuits are designed to perform reliably in the challenging conditions of a vehicle, where factors like vibration, temperature fluctuations, and long-term use are common.
Future Trends and Innovations
The future of flex PCBs is as flexible as the boards themselves. Emerging technologies in materials and fabrication methods continue to push the boundaries of what’s possible. The fast PCB prototyping service is particularly crucial in experimenting with new designs and concepts, speeding up the innovation process.
As wearable technology and IoT devices become more prevalent, the role of flex PCBs in these sectors is expected to grow. Their ability to fit into irregular spaces and conform to various shapes makes them an ideal choice for these cutting-edge applications.
Challenges and Considerations
While the advantages of advanced flex circuits are many, they also come with their own set of challenges. Design complexity, manufacturing precision, and cost considerations are just some of the hurdles that PCB assemblers and manufacturers face.
Sustainability is another critical aspect. As the demand for electronic devices grows, so does the need for environmentally friendly manufacturing processes. Leading PCBA manufacturing companies are increasingly focusing on reducing their environmental impact while maintaining high standards of quality.
Conclusion
Advanced Flex PCBs represent a significant leap in electronic design and manufacturing. Their flexibility, combined with the expertise of the best PCB manufacturers, has opened up new possibilities in various fields. As technology continues to advance, we can expect even more innovative applications and improvements in flex PCB technology.
Arisentec, founded in 2011 and headquartered in Shenzhen, China, is a leading electronic product and service enterprise. They specialize in intelligent mobile terminals, PCB design, fabrication, parts sourcing, and PCBA. Arisentec is known for its extensive supplier resources, comprehensive supply chain management, and products used in various industries like telecom, medical, industrial control, smart home, and IoT. The company has a global presence, serving over 3,000 customers in more than 30 countries, and is renowned for its innovative solutions and high-quality services.u003cbru003eFor more details, visit their u003ca href=u0022https://arisentecpcb.com/u0022u003ewebsiteu003c/au003e.
arisentec